GreenStaxx Advantages
Standardization and Replication: The construction industry is plagued by inefficiencies that stem from "one-off" project designs and "start from scratch" processes. GreenStaxx is disrupting this business-as-usual model by offering individual unit plans as ready-to-go products complete with CD-level engineering and specification. These unit plans can be included in various multifamily building designs to achieve breakthroughs in cost and quality compared to typical construction.
Simplicity and Predictability: The GSX System allows replication of well-vetted unit designs across multiple projects, leading to fewer mistakes, tighter construction schedules, and continuous refinement of the workflow among project partners. We’re reorganizing the multifamily construction process and swapping an industry-wide problem of one-off projects and teams with a system that reaps the benefits of replication.
Sustainability and Quality: We think natural, high-quality materials and energy-efficient systems are a better definition of luxury. GSX units can be built to Passive House standards. Our standardized outline specification prioritizes what’s good for people and the planet, and our coordinated supply chain ensures these options are affordable. GSX units are successful in high-rent markets and have won multiple awards for tenant satisfaction and design excellence.
Speed & Savings: Our pre-engineered, standardized unit-plans reduce time-intensive decision-making and rework* on common components of multi-family construction. We assemble seamless project teams with Architects, Modular Manufacturers and Construction Managers to enable Developers to achieve cost savings of up to 20% of total project costs**, and more with each subsequent project. Our researched and coordinated outline specification is optimized for taking advantage of state and federal subsidies.
* Rework typically adds 5% to overall project cost and an average of almost 10% to schedule.(Navigant)
** Modular construction can speed construction by as much as 50% and cut costs by up to 20% (McKinsey)

Advantages of Modular Construction
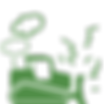

Reduced waste: Modular construction involves the factory production of building components, where materials are precisely measured and cut, resulting in up to just 1.8% waste compared to 30% with traditional construction methods (source). The controlled factory environment allows for efficient material usage and recycling or repurposing of excess materials.
Reduced site disruption: Since modular construction occurs off-site in a factory, on-site disruption is minimized. This reduces dust, noise, and traffic congestion, which can be particularly important in urban areas. It also minimizes the environmental impact of transporting materials and construction activities to and from the site.
Faster construction timeline: Modular construction techniques enable faster construction timelines than conventional methods. A considerable portion of the building is manufactured concurrently with site preparations, and time is further saved due to reduced coordination needs and reliance on weather conditions.
Enhanced quality control: Factory-controlled environments in modular construction ensure strict quality control measures. Construction materials are thoroughly inspected, modules are reviewed at each step of the process, and adherence to building codes and standards is closely monitored. This precision reduces the chances of defects, resulting in higher quality and longer-lasting buildings.